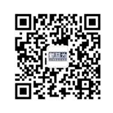
微信公眾號二維碼
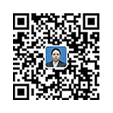
微信咨詢顧問二維碼
新益為精益生產(chǎn)咨詢公司概述:精益生產(chǎn)管理方式源于日本豐田,風(fēng)靡全球,雖然精益生產(chǎn)管理最初源于制造車間,但衍生至今,其應(yīng)用范圍已遠(yuǎn)遠(yuǎn)超越這一范圍,今天我們就來探討一下精益生產(chǎn)管理在制造業(yè)設(shè)計(jì)部的應(yīng)用。
精益生產(chǎn)管理方式
一、精益生產(chǎn)管理在設(shè)計(jì)部門開展可視化管理
從20世紀(jì)80年代起,除了專注于“準(zhǔn)時化”和“自慟化”兩大支柱的活動推進(jìn),豐田汽車也進(jìn) 一步豐富了精益生產(chǎn)管理的體系思想。這其中,就包含了重視“人”的要素的可視化管理。
1、可視化管理的含義
在日本式精益生產(chǎn)管理中,可視化,不僅僅是將目標(biāo)、進(jìn)度、實(shí)際狀況展示在管理板上,而是通過這些內(nèi)容的可視化,實(shí)現(xiàn)信息共享,讓管理者監(jiān)督者與員工的工作真正地聯(lián)動起來。
2、設(shè)計(jì)部門中的可視化管理
這一機(jī)制在設(shè)計(jì)研發(fā)部門同樣可以得到運(yùn)用。設(shè)計(jì)研發(fā)部門的主要工作形態(tài)是每一個人每天大約80%的時間都是獨(dú)自面對電腦,用電子郵件的形式傳達(dá)著各種信息。這種工作形態(tài)、下,必要的信息是否及時地傳達(dá)給了強(qiáng)相關(guān)人員,亟待解決的問題是否及時地得到了回復(fù),往往很難確切地知道。即便在日本,精益生產(chǎn)管理這一效率技術(shù)廣泛被應(yīng)用的國家,也仍然有企業(yè)出現(xiàn)了這樣的聲音:“我 不知道上司交給我的工作指令是、什么目的”“我不知道我的部門領(lǐng)導(dǎo)今天的行程是什么”“我不知道坐在我隔壁的同事每天都在處理哪些工作”等等。類似
這種問題,不妨將昨天、今天、明天的每一個人的工作明確地寫在白板上,可視化不是目的,目的在于通過可視化,看出每、一個人的、工作負(fù)荷量,使得團(tuán)隊(duì)在每天的集會時能夠做出協(xié)調(diào)與調(diào)整。
另外,設(shè)計(jì)部門的工作并不像制造部門有實(shí)際的流水線、產(chǎn)品等有形載體,而是無形而繁雜,可視化管理有一個好處,就是將這些默然于心的工作流程用管理板的方式羅列出來,幫助設(shè)計(jì)人員找到其中沒有附加價值的工作以及計(jì)算出此類工作花費(fèi)的時間,從而找到改善的著眼點(diǎn)與目標(biāo),縮短設(shè)計(jì)的周期。而這里的可視化管理,更多的是一種自發(fā)性地發(fā)現(xiàn)問題,改善問題,有助于設(shè)計(jì)人員的能力提升。
二、精益生產(chǎn)管理自工序完結(jié)在設(shè)計(jì)部門的應(yīng)用
1、精益生產(chǎn)管理自工序完結(jié)的含義
精益生產(chǎn)管理的兩大支柱之一,自慟化, 直接含義是“一旦出現(xiàn)異常就能停止下來”。它的含義是,不在最終工序設(shè)置檢驗(yàn)工序,而是在制造過程中的每一個工序,從人、設(shè)備、材料、作業(yè)方法以及自我檢驗(yàn)這五方面確保該工序的質(zhì)量,保證流到下一個、工序的是合格品,從而達(dá)到即便沒有最終檢驗(yàn)也能產(chǎn)出合格品的水平。自工序完結(jié)的導(dǎo)入,使豐田汽車的不良率從百分之十,下降到了百萬分之五的水平。
2、自工序完結(jié)在設(shè)計(jì)部門如何具體展開
第一步,明確出自己的工作目的是什么。
第二步梳理出工作流程,目的是看清楚自己負(fù)責(zé)的設(shè)計(jì)工作,以及前后銜接的工作分別是什么。
第三步,將自己負(fù)貴的設(shè)計(jì)工作分解成要素作業(yè),即具體的開展步驟。
第四步,整理出每一項(xiàng)要素作業(yè)的輸入與輸出。這一步非常之關(guān)鍵,“輸入” 代表的是進(jìn)行這一步動作的良品條件,可以從信息收集、負(fù)責(zé)人的能力、手法、工具等多個維度考察“輸入”是否完備,是否足以支撐這一步動作保質(zhì)保量的完成:而“輸出”則表示判斷基準(zhǔn),當(dāng)這一步動作完成時,運(yùn)用什么方法檢驗(yàn)完成的結(jié)果,例如使用確認(rèn)表,進(jìn)行評審等。確立“良品條件”與“判斷基準(zhǔn)”是設(shè)計(jì)工作實(shí)現(xiàn)自工序完結(jié)的核心步驟,對應(yīng)制造環(huán)節(jié)來說,“良品條件”就是人、設(shè)備、材料、作業(yè)方法,而“判斷基準(zhǔn)”就是自我檢驗(yàn),在工作完成的當(dāng)下就能夠確認(rèn)質(zhì)量。
第五步,將以上內(nèi)容應(yīng)用到實(shí)際業(yè)務(wù)中,并標(biāo)準(zhǔn)化,形成工作指南,出現(xiàn)變化以及問題時,再從第一步開始進(jìn)行梳理, 如此循環(huán)。由此,設(shè)計(jì)工作的每一個步驟都有明確的工作指南,無論是經(jīng)驗(yàn)豐富的設(shè)計(jì)人員,還是剛進(jìn)入行業(yè)的新人,都能清楚地知道:開展某
項(xiàng)設(shè)計(jì)工作時,我應(yīng)該干什么,需要什么輸入,如何檢驗(yàn)。
4、自工序完結(jié)導(dǎo)入的意義
自工序完結(jié)強(qiáng)調(diào):只要是本工序的后工序,都是本、工序的客戶。讓客戶滿意是每一項(xiàng)工作的最基本要求。 在設(shè)計(jì)研發(fā)這樣的職能部門,常常遇到這樣的情況:設(shè)計(jì)人員埋頭苦干地趕出了圖紙,結(jié)果技術(shù)部門提出了很多意見,又需要重新修改,返工數(shù)遍,積極性受到打擊。而導(dǎo)入自工序完結(jié)機(jī)制以后,要求各環(huán)節(jié)人員審視開展工作前的準(zhǔn)備是否充分,工作結(jié)束后要及時并做有效的確認(rèn),也就能避免上述情況了。
除此之外,還有很多的優(yōu)點(diǎn),比如說因?yàn)橛辛嗣鞔_的工作指南,減少了失敗和妥協(xié)的情況:通過梳理良品條件與判斷基準(zhǔn),能看出違背原理原則的地方等等。
現(xiàn)如今的精益生產(chǎn)管理已經(jīng)衍生至各個國家的各行各業(yè),為我們的企業(yè)管理帶來了極大的幫助,精益生產(chǎn)管理不是一個死的管理體系,它可以隨著時代的發(fā)展而進(jìn)步,相信隨著科技的進(jìn)步,精益生產(chǎn)管理會越來越好。
建立生產(chǎn)有序、管理順暢,操作規(guī)范,士氣高昂、高質(zhì)量、低成本、短交期的作業(yè)現(xiàn)場;
為企業(yè)規(guī)劃設(shè)計(jì)一套由內(nèi)到外的形象升級,外觀視覺價值體現(xiàn)、內(nèi)在的管理內(nèi)涵體現(xiàn);
全員參與設(shè)備管理高產(chǎn)出和低成本運(yùn)營,提升設(shè)備管理能力,維護(hù)能力,提高效率
構(gòu)建班組生產(chǎn)管理體系、循環(huán)評價、人才育成、持續(xù)改善、績效管理、文化養(yǎng)成體系;
提高產(chǎn)品質(zhì)量、降低生產(chǎn)成本、縮短交期、增加利潤,讓管理更系統(tǒng)科學(xué),執(zhí)行力更強(qiáng)
對工廠的各個組成部分進(jìn)行合理安排,以提高生產(chǎn)效率、降低成本、優(yōu)化物流、改善工作環(huán)境等